La Transformación Digital está revolucionando la manera en que las empresas de manufactura operan a nivel global. Este fenómeno se refiere a la integración de tecnologías digitales en todas las áreas de una organización, cambiando fundamentalmente cómo se entregan los productos y servicios, y cómo se optimizan los procesos internos.
En el sector manufacturero, este cambio ha sido especialmente impactante, ya que las fábricas y líneas de producción tradicionales están adoptando nuevas tecnologías como el Internet de las Cosas (IoT), la inteligencia artificial (IA) y la automatización robótica para mejorar su eficiencia, reducir costos y aumentar la calidad de sus productos. Si bien las oportunidades que ofrece la Transformación Digital son inmensas, muchas empresas enfrentan retos importantes para implementarla de manera efectiva.
En la manufactura, la Transformación Digital no es solo una tendencia, sino una necesidad para mantenerse competitivo en un entorno de constante cambio. Las empresas que no adopten las herramientas digitales corren el riesgo de quedarse atrás, ya que sus competidores mejoran continuamente sus procesos con tecnologías avanzadas. Además, la digitalización está permitiendo una mayor personalización de los productos y un tiempo más rápido de entrega, lo que resulta en una experiencia del cliente más satisfactoria.
Sin embargo, para muchas empresas de manufactura, implementar la Transformación Digital no es tan simple como añadir una nueva máquina a su línea de producción; implica una reestructuración total del enfoque de negocio, tanto en la cultura empresarial como en los sistemas tecnológicos utilizados.
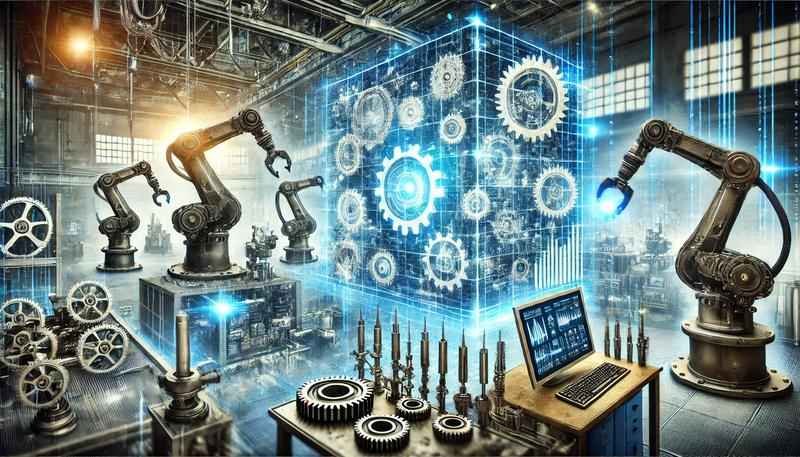
¿Qué es la Transformación Digital en la Manufactura?
La Transformación Digital en la manufactura se refiere a la adopción de tecnologías digitales para mejorar la eficiencia, la flexibilidad y la capacidad de adaptación en los procesos de producción. Estas tecnologías permiten a las empresas recopilar y analizar datos en tiempo real, automatizar tareas repetitivas y tomar decisiones más informadas basadas en análisis predictivo. Las fábricas inteligentes, o Smart Factories, son un claro ejemplo de cómo la digitalización está cambiando la manufactura. En estas instalaciones, las máquinas están conectadas entre sí y con sistemas de control centralizados, lo que permite una producción más flexible y eficiente.
Algunas de las principales tecnologías que impulsan la Transformación Digital en la manufactura incluyen:
- Internet de las Cosas (IoT): El IoT permite a las máquinas y dispositivos en una planta de producción comunicarse entre sí y enviar datos en tiempo real a una plataforma centralizada. Esto facilita la monitorización de los equipos y la predicción de fallos antes de que ocurran.
- Inteligencia Artificial (IA): La IA se utiliza para optimizar los procesos de producción mediante el análisis de grandes cantidades de datos y la toma de decisiones automatizadas.
- Automatización: La automatización permite reducir los errores humanos y aumentar la velocidad de producción.
Beneficios de la Transformación Digital en la Manufactura
La Transformación Digital ofrece múltiples beneficios a las empresas de manufactura que la implementan de manera efectiva. Estos beneficios no solo impactan en la eficiencia operativa, sino también en la calidad del producto final y la satisfacción del cliente. Entre los beneficios más destacados están:
1. Mayor eficiencia operativa
Con la ayuda de tecnologías digitales, las empresas pueden optimizar sus procesos de producción y reducir el tiempo de inactividad de sus equipos. El uso de sensores y sistemas conectados a través del IoT permite monitorear en tiempo real el estado de las máquinas, lo que a su vez facilita un mantenimiento predictivo. Esto significa que las reparaciones o ajustes pueden realizarse antes de que ocurra una falla, evitando interrupciones costosas en la producción.
2. Reducción de costos
La automatización de procesos no solo reduce los errores humanos, sino que también disminuye la necesidad de intervención manual en la producción. Esto resulta en una reducción significativa de costos laborales, al tiempo que se incrementa la productividad. Además, la capacidad de predecir y prevenir fallos en las máquinas reduce los costos de mantenimiento y prolonga la vida útil del equipo.
3. Mejora en la toma de decisiones
El análisis de datos en tiempo real permite a los gerentes y operadores tomar decisiones más informadas y basadas en hechos concretos. Las herramientas de análisis predictivo, impulsadas por la inteligencia artificial, permiten prever posibles problemas en la línea de producción y ajustar los procesos para evitar errores o defectos en el producto final.
4. Personalización del producto
La digitalización permite a las empresas de manufactura adaptar sus líneas de producción para crear productos personalizados. Gracias a la fabricación flexible y al uso de tecnologías como la impresión 3D, las fábricas pueden responder más rápidamente a las demandas específicas de los clientes sin sacrificar la eficiencia o la calidad.
Herramientas Clave para la Transformación Digital en la Manufactura
Implementar una Transformación Digital exitosa en la manufactura requiere el uso de varias herramientas tecnológicas que permiten a las empresas optimizar sus procesos y adaptarse a los cambios del mercado. A continuación, se presentan algunas de las herramientas más importantes para lograr este objetivo:
1. ERP (Enterprise Resource Planning)
Los sistemas ERP son fundamentales para gestionar los recursos de la empresa de manera eficiente. Estos sistemas permiten integrar todos los aspectos de la producción, desde la gestión de inventarios hasta la planificación de la producción y la contabilidad. Un ERP bien implementado puede mejorar la visibilidad de los procesos y permitir una toma de decisiones más eficiente.
2. MES (Manufacturing Execution Systems)
El MES es una plataforma que controla y gestiona las operaciones de producción en tiempo real. A través de esta herramienta, las empresas pueden supervisar todas las etapas de la producción y asegurarse de que se cumplan los estándares de calidad. Además, el MES permite recopilar datos sobre el rendimiento de las máquinas y los operarios, lo que facilita la optimización continua.
3. Sistemas de mantenimiento predictivo
Los sistemas de mantenimiento predictivo utilizan datos en tiempo real y análisis avanzados para predecir cuándo es probable que falle un equipo o una máquina. Esto permite a las empresas realizar el mantenimiento antes de que ocurra una avería, lo que reduce el tiempo de inactividad y mejora la eficiencia general.
Estrategias para Implementar la Transformación Digital en la Manufactura
Adoptar la Transformación Digital en la manufactura no es un proceso simple. Implica una cuidadosa planificación y una implementación estructurada. Aquí algunas estrategias clave para lograr una digitalización efectiva:
1. Evaluar las necesidades y capacidades actuales
Antes de implementar cualquier tecnología, es importante realizar una evaluación exhaustiva de los sistemas y procesos actuales. Esto ayudará a identificar qué áreas pueden beneficiarse más de la digitalización y dónde es necesario hacer cambios.
2. Formar al personal
La Transformación Digital no solo implica la adopción de nuevas tecnologías, sino también la formación del personal para que pueda utilizar estas herramientas de manera efectiva. Proporcionar capacitación continua es crucial para garantizar que los empleados puedan adaptarse a las nuevas tecnologías y maximizar su rendimiento.
3. Establecer metas claras
Es esencial definir qué se espera lograr con la Transformación Digital. Ya sea mejorar la eficiencia, reducir costos o personalizar productos, tener metas claras ayudará a guiar el proceso y a medir el éxito.
4. Monitoreo y mejora continua
Una vez implementada la Transformación Digital, es importante monitorear continuamente los resultados y hacer ajustes donde sea necesario. La digitalización no es un evento único, sino un proceso en evolución.
El Futuro de la Transformación Digital en la Manufactura
La Transformación Digital en la manufactura no es una tendencia pasajera, sino el futuro del sector. A medida que las tecnologías avanzan y se integran de manera más profunda en los procesos productivos, las empresas que no adopten estos cambios corren el riesgo de quedarse rezagadas. Las fábricas del futuro serán más conectadas, más eficientes y más adaptables, lo que permitirá a las empresas responder de manera más ágil a las demandas del mercado y a las expectativas de los consumidores.
Sin duda, la Transformación Digital ha llegado para quedarse, y aquellas empresas que inviertan en ella estarán mejor posicionadas para competir en un entorno global cada vez más dinámico.